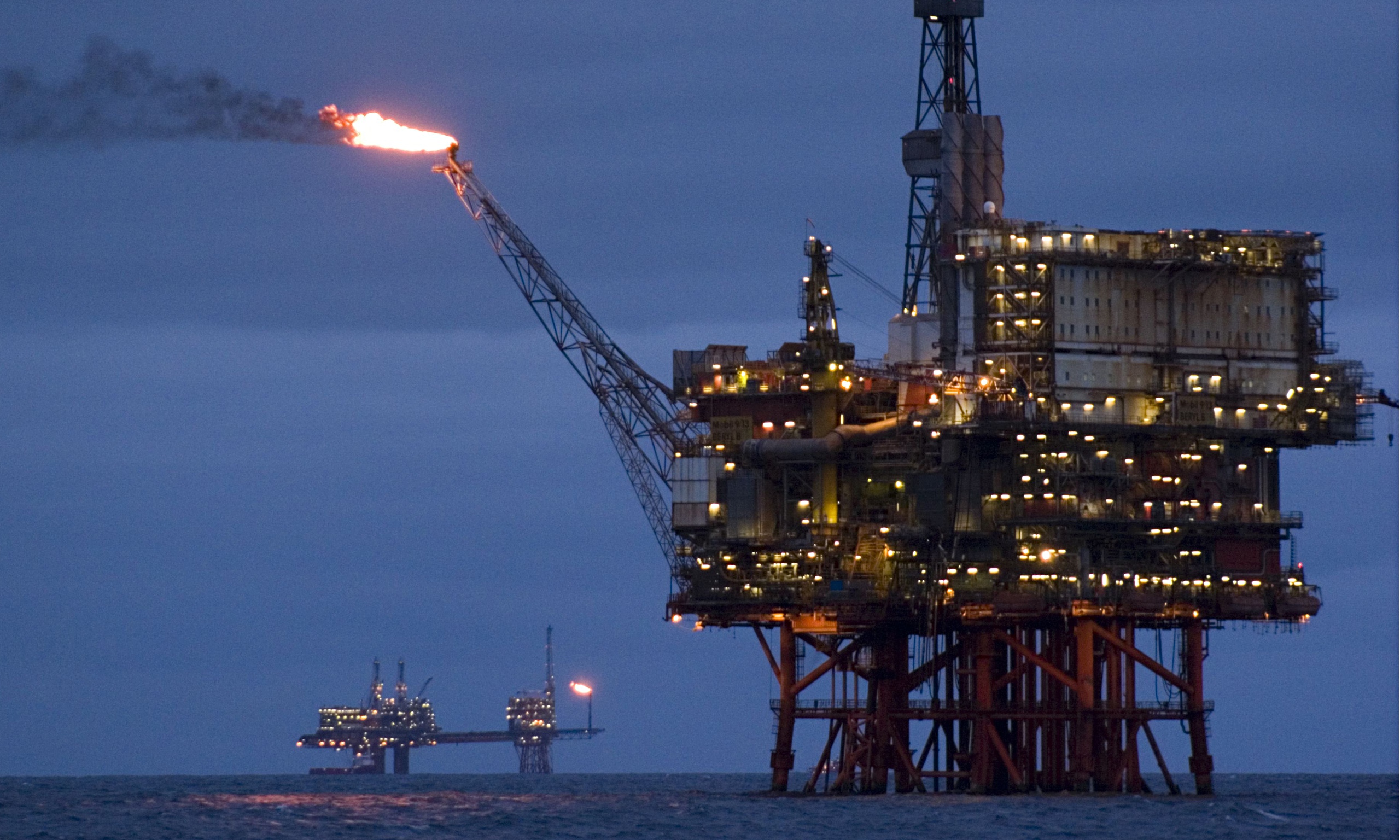
The Service, Maintenance and Repair of Oil Rig Chillers
We use steel shipping boxes to send all of the necessary equipment for the maintenance of oil rig chillers.
0161 237 3727
service@maximuschillers.com
Oil rig chillers are a challenge to any chiller company. The sea causes corrosion issues to accelerate on the pipework and the heat exchangers. The remote location is a challenge too as you can’t just pop out to the suppliers for a spare part. Therefore, a higher level of maintenance needs to be carried out alongside the meticulous planning of a service visit. Each aspect of the job is thought through in detail, then all of the necessary parts and materials are checked off one at a time into our shipping boxes. These boxes are robust enough to survive the adverse conditions encountered on the way to the repair. Read below for an insight into how we at Maximus Chillers get the job done correctly on the various types of plant found on an oil rig…
Offshore & Marine Chillers- Maintenance
Chillers located offshore are maintained so that they can stand up to the most extreme marine environments. They are therefore built very robustly.
Sea Water Condenser Cooling
Sea water can be used to cool the condenser as it is often very cold and in close proximity to the plant. Pumps are used to suck the sea water up and through shell and tube heat exchangers. The heat exchangers have to be able to cope with not only the sea water being pumped through, but the accumulation of marine life.
Filtration Systems
Therefore, filtration systems are used and periodic maintenance is carried out to the inlet, outlet and tubes.
Tube Cleaning
Where necessary, equipment and chemicals are used to keep the heat exchange across the tubes in the best condition.
Plant Room
This kind of chiller is usually located in a plant room which is close to the stores. This makes maintenance to the chiller a lot easier as spare parts and materials are nearby. Also in the plant room are the associated pump sets and pressurisation unit. There are two pump sets: one for the condenser cooling sea water and the other to supply chilled water to the living quarters…
Living Quarters
The accommodation block is cooled by the chilled water which has been pumped up from the chiller plant room. It feeds a fan coil unit in each room which is operated by a thermostat on the wall. When the room temperature rises above a deadband of several degrees, the switch closes in the thermostat and volts continue to a solenoid valve. When this solenoid valve lifts, chilled water flows through the fan coil unit. The fan blows across the coil and cools the room down. Heat energy from the room is absorbed into the chilled water. On achieving set point, the switch in the thermostat drops out, the solenoid shuts down and the fan coil stops cooling. The filters need to be changed at periodic intervals by our dedicated maintenance engineers.
0161 237 3727
service@maximuschillers.com
Hydrocarbon Liquefaction Chiller Service
Hydrocarbon chiller service is required because the gas coming up stream needs to be cooled into its liquid state. This is because the volume of liquefied hydrocarbons is around 600 times smaller than in their gaseous state. The liquifying process aids the removal of dust, water and heavier compounds.
Liquefied Natural Gas
This LNG can then be transported easily back to shore for further processing. It is composed mainly of propane, butane, ethane and methane.
Hazards for Oil Rig Chillers
This liquefied gas is colourless, odourless, non corrosive and non toxic. Of course, the main hazard with hydrocarbon liquefaction is the fact that it is a flammable substance. The heat exchanger is manufactured to be intrinsically safe so that sparks cannot be produced which cause an explosion.
How it Works
The chiller refrigerant is expanded through a shell and tube heat exchanger which causes a low temperature condition to exist. This low temperature causes the gas on the other side of the heat exchanger to condense and run down. The newly formed liquid then discharges from the chiller.
Service of Gas Liquefaction Oil Rig Chillers
When service work is being carried out to gas liquefaction chillers, explosive atmosphere protection equipment and procedures are used. If everything goes as it should there should be minimal risks involved. This is because the hydrocarbon gas is on the other side of the heat exchanger. Also, the gas being liquefied can be isolated and locked off.
Portable Explosive Gas Detectors
Each of our engineers is issued with a gas detector suitable for use with hydrocarbons. These detectors are periodically sent off for calibration. Interim calibration and testing is carried out while on site with our bump testing rig and spare parts. Our uniform is fitted with a special attachment fitting for the detectors.
Intrinsically Safe Test Equipment
Our multi meters, digital thermometers and ammeters have isolated battery compartments for spark free use. Our test leads are fused for extra protection to our engineers.
Case Study of Oil Rig Chillers
One of our offshore customers was experiencing high pressure problems on a small water cooled chiller. The onsite engineers changed the condenser with a spare one from their stores. They decided to ship the condenser needing repairs to our Head Office. On arrival, the water inlet and outlet manifolds were removed. There was found to be an accumulation of organic material as sea water was the cooling medium. We used our specialist equipment to repair the condenser, then we shipped it back to the oil rig.
Next Steps…
Give us a bell on 0161 237 3727
service@maximuschillers.com to drop us a line.
Contact Form works and is monitored- try it!
What We Offer for Oil Rig Chillers
Highly skilled engineers.
Calibrated, high quality equipment.
An easy to deal with, non political company.
Why Choose Us for Oil Rig Chillers?
We have a network of overseas customers around the world. Therefore, we are used to solving problems in remote locations. All aspects of the job are planned to ensure everything goes smoothly.

Call Out
Schedule a site visit today!