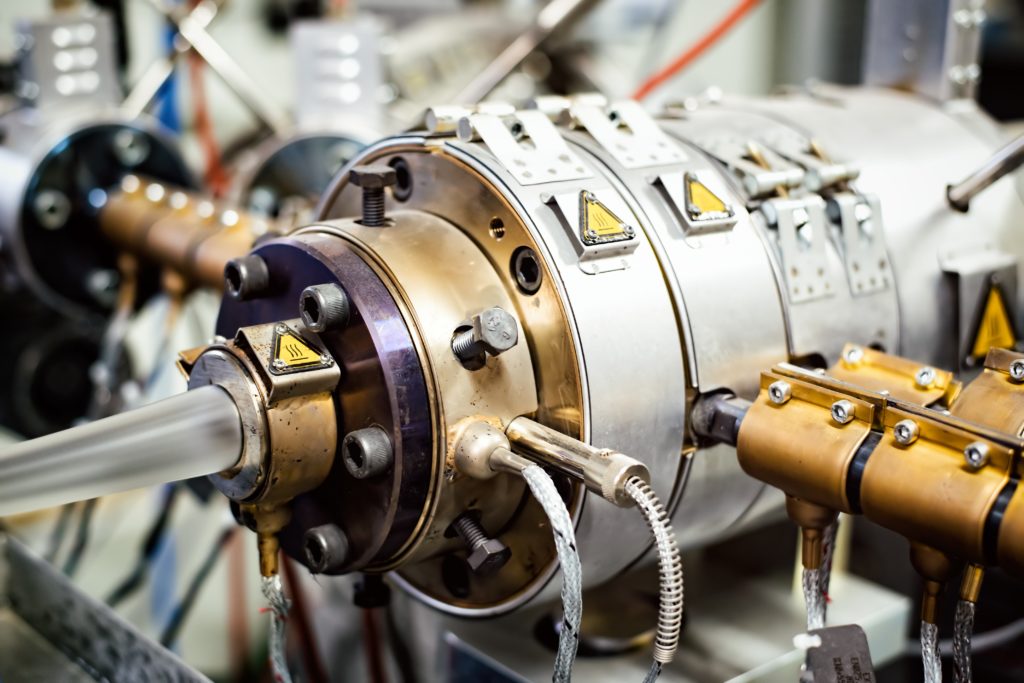
The Service, Maintenance and Repair of Plastic Extrusion Moulding Chillers
Maximus Chillers have the expertise to maintain a reliable supply of chilled water from plastic extrusion moulding chillers.
0161 237 3727
service@maximuschillers.com
The water temperature supplied is usually quite high and varies depending on the product being produced. The most common types of products are plastic pipe, PVC window frames and plastic bars. However, there are a diverse range of other products that can be made using this process.
Cooling Tanks
After the product is extruded from the die head, it goes through several cooling tanks. This is to control the cooling of the product and so preventing it from warping and bending. The chilled water is usually gravity fed into the tanks and is sprayed around the product as it goes through. It then drains down into a return pipe and back into the process tank.
Process Tank
This is a mixing vessel that has the water supplied to the cooling tanks and the water supplied from a plate heat exchanger. It allows for a steady temperature to be supplied to the cooling tanks as the PHE water system is considerably cooler than the return water.
PHE
The plate heat exchanger water system provides a step in between from the process tank and the chiller water system. This is because the process water is contaminated with plastic coming from the process. If these impurities found their way into the chiller evaporators, they would cause a loss of heat exchange due to thermal insulation. They would also reduce the life span of the chiller evaporator. The temperature of the PHE water system is usually around 15°C.
Plastic Extrusion Moulding Chiller Water System
This is the cleanest part of the plant with a strainer usually being fitted to the inlet of the evaporators. The temperature of the chilled water is usually around 10°C. To add volume to this water system, a buffer vessel or tank is often included. The chillers load up in response to more lines coming into operation in the factory.
Why Choose Us for Plastic Extrusion Moulding Chillers?
Each company vehicle carries the same state of the art equipment. This is to ensure that the job goes well, whatever happens. We also carry everything from spare fuses to compressor contactors. This means that we are not likely to have to have to go to the suppliers whilst on site. We are therefore on site longer to get the job done quicker.
0161 237 3727
service@maximuschillers.com
What We Offer for Plastic Extrusion Moulding Chillers
A network of engineers around the UK and an overseas engineer for the commissioning of this kind of plant around the world.
A friendly service and a no nonsense company that you can get on with easily.
Risk Assessment Method Statements are supplied after a site survey to control the risks. These work hand in hand with your permit to work to minimise the chances of injury.
High quality personal protective equipment carried by each engineer. This means our engineers are fully capable of complying with your safety requirements.
Case Study of Plastic Extrusion Moulding Chillers
We attended site at a plastic extrusion moulding customer of ours in Darbyshire to carry out the periodic chiller maintenance. As the factory was in production, we did this using non destructive testing. This is because we did not want a chiller failure to occur. That would be the worst case scenario for a chiller service company: you arrive on site to do a job to a working chiller, then you have to tell the onsite engineer that the chiller will be off for days while a repair is being carried out!
Compressor Run Amps of Plastic Extrusion Moulding Chillers
We checked the current of the compressors by temporarily lowering the set point of the machine. Each compressor was a hermetically sealed scroll with rotolock fittings. A current reading of 48 to 53 amps was recorded across the 6 the compressors. This variation was due to the difference in discharge pressure at the time of taking each of the readings. The higher the pressure, the higher the amps drawn.
Superheat and Subcooling of Plastic Extrusion Moulding Chillers
Taking advantage of the lowered setpoint, our engineer then checked the superheat and subcooling values of the machine. Both systems had nominal readings in line with industry guidelines.
Oil Return of Plastic Extrusion Moulding Chillers
System 1 had a slightly low oil level at the beginning of the maintenance. This system had been set as the lag system. The run at 100% brought the oil back to the compressor to the correct level.
Lead/ Lag of Plastic Extrusion Moulding Chillers
Our engineer then changed this system to the lead system in the chiller controller. He rotates the lead/ lag on each maintenance visit to balance the wear on the compressor bearings.
Tick Sheet
We believe we have the most detailed Tick Sheet in our industry. Our engineer went through the list of checks and recorded all of the readings on our sheet. Building up a history gives us an insight into faults that take a long time to develop. We can look for the deterioration in the readings over several maintenance visits. Each tick sheet is scanned and sent into our Head Office in Manchester at the end of each visit. It is then forwarded to site along with a detailed report of our findings.
F-gas Register
Last but not least, we always complete the on site F-gas register on each visit. This details the leak tests, refrigerant removals, refrigerant additions and follow up leak tests. It can then be submitted to an external auditor attending site to see if the correct procedure is being followed.
Next Steps...
0161 237 3727 for an informal chat to find out your issues.
service@maximuschillers.com to send us your pictures and PDFs.
✎Contact Form works and it is also monitored- try it!

Call Out
Schedule a site visit today!