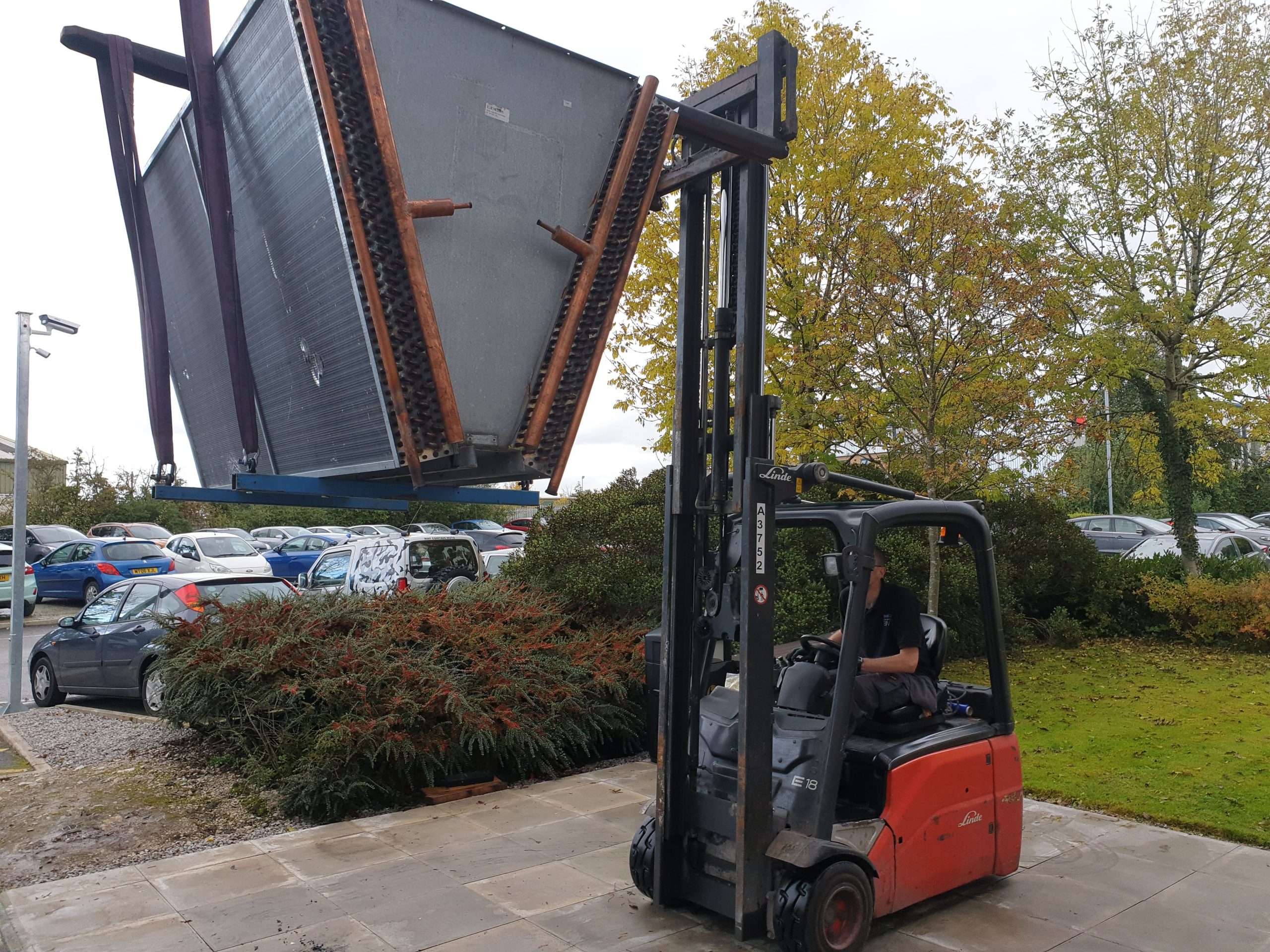
Chiller Retrofitting Company
Chiller retrofitting is a prudent choice as the cost of a new chiller is expensive, not to mention the installation costs. This money can be spent on driving your business to the next level. We at Maximus Chillers are adept at retrofitting any part to your plant. We will make your old chiller as efficient as a new one.
Retrofitting Chiller Condensers
Any size and thickness of condenser can be built to your bespoke specifications. Standard and micro channel condensers are made to measure then delivered to site.
Retrofitting Chiller Evaporators
Shell and tube evaporators and plate heat exchangers are selected and matched to the exact approach and superheat specifications of the existing plant.
Retrofitting Chiller Metering Devices
All manuals are available to our highly trained engineers for the selection of expansion valves and ammonia float valves.
Retrofitting Chiller Components
Solenoid valves, fans, flow switches, oil heaters, compressors etc. are available- often same day.
Retrofitting Low GWP Chiller Refrigerants
Alternative refrigerants are available to 'drop in' to your existing plant. Our engineers can adjust the subcooling and superheat values to keep your plant running seamlessly as before.
Retrofitting Chiller Controls
In our controls laboratory, controllers and PCBs are repaired, or the software downloaded into a new controller: visit chiller upgrade to read more. We also have the capability to fit new, state of the art, inexpensive controllers with all the associated sensors, transducers and relay boards. We have the capability to do this to any machine.
0161 237 3727
service@maximuschillers.com
Why Choose Us for Chiller Retrofitting?
National and Global
We have a network of engineers at locations around the UK, so an engineer is only a couple of hours away. Around the world, we have a network of customers as we extend the life of plant- saving the cost of replacement.
Any Chiller- Any Problem- Any Part- Any Refrigerant- Anywhere- The MAXIMUS ADVANTAGE™
Engineers Second to None
Each engineer has attended 4 years at college to achieve NVQ 3/ City & Guilds in Complex Systems. Our engineers are trained in the safe handling of HFC, HFO and Ammonia.
Reliable Service
If the job is on the calendar: you are the Number 1 priority. We will not leave site until we have resolved all of your issues.
What We Offer for Chiller Retrofitting
Our service provides massive cost savings relative to the purchase of new plant.
No installation costs.
Seamless operation of your existing plant through exact match retrofitting.
Same efficiency as a new chiller by fitting variable speed drives and the use of low GWP refrigerants.
No CO2 emissions in the construction of new chillers. This amount is never included in the efficiency figures for a new chiller.
Case Study of Chiller Retrofitting
We retrofitted the chiller ‘v’ condenser in the picture. See below for the start to finish operation…
Site Survey
Our engineers attended site to take measurements and photos, these were then returned to our factory.
Design
The exact design specifications of subcooling and air flow rate were worked out by our computer software. This was to ensure that the new condenser had the same performance characteristics as the old one.
The Chiller Lid and Condenser Removal
There was no refrigerant in the system due to the leak. This saved the time taken for the decant process. The 2 fan decks were bolted onto the chiller lid. The bolts around the chiller lid were removed and the fan wiring disconnected. Lifting accessories were set up, a forklift truck was used to lift the lid clear of the chiller, then take it to a storage area.
Adapting and Replacing the Condenser
The 5mm bottom flange, running along the new condenser had to be cut at the points where it attached to the frame of the condenser. This had not been considered during the design phase as it was concealed from view by the condenser. Lifting equipment and a forklift truck located both halves of the ‘v’ condenser into place.
Brazing of Discharge and Liquid Pipes
The discharge and liquid stubs from the new condenser come complete with test ports from the factory. These test ports were used for the factory strength test of 26 bar. The condensers had been shipped with a 2 bar holding charge. The stubs were cut to size and the existing pipework married into the new. The brazing job went seamlessly, ready for the next phase of the job…
BSEN 378 Leak Tightness Testing
This standard of pressure testing requires a steel braided hose and ¼ turn shut off valve. The leak tightness test was carried out according to standard industry guidelines.
The Drying Out Process
This was conducted overnight as there is nothing more boring than watching a Torr gauge slowly coming down. Our engineer returned in the morning to a vacuum of 1.5 Torr. This is the same pressure as if the Torr gauge were to be fitted directly on to the vacuum pump.
Subcooling Analysis
A fan speed controller is fitted to the machine which speeds up with increasing pressure. During run testing: refrigerant was charged into the liquid side of the evaporator. This, in turn, increased the pressure in the condenser. The subcooling value increased to the optimum level and the machine went back into operation.
Next Steps...
Talk to our technical support engineer about the project on 0161 237 3727
Drop us a line service@maximuschillers.com
Our Contact Form works and is monitored- try it!
Call Out
Schedule a site visit today!