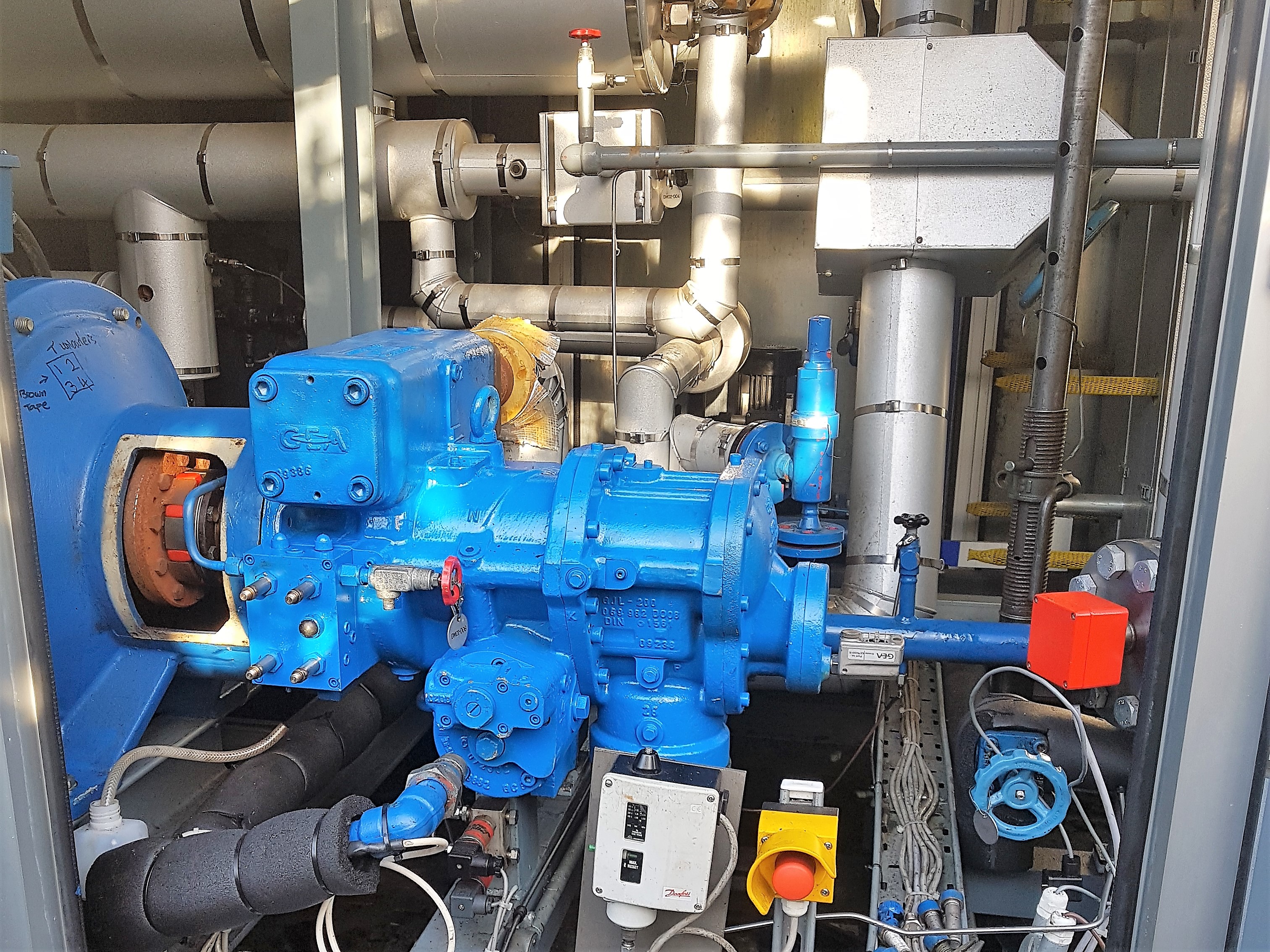
Industrial Refrigeration Capability
Maximus chillers is second to none in the field of industrial refrigeration.
Any Chiller- Any Problem- Any Part- Any Refrigerant- Anywhere- The MAXIMUS ADVANTAGE™
Past
Ammonia has been used for low temperature applications for over 125 years and has a reputation as a pre eminent refrigerant. Ammonia is used in applications such as food production. CFCs, such as Freon, became popular in the 1930s due to their low toxicity. The chlorine in the refrigerant was found to have caused a hole in the ozone layer. Therefore, they have now been phased out. Non chlorine, low toxicity, HFCs were developed to replace the CFCs.
Present
HFC refrigerants have a high global warming potential, so they are being phased down to 21% by 2030.
HFO refrigerants, such as R1234ze are used for chilled water and process applications.
Ammonia is the best choice of refrigerant for industrial applications.
Future
A new ammonia plant is simpler in design, therefore competitive in price to HFC. The higher initial cost is paid back in electricity savings within 2 years- then they become cheaper. They use less electricity because ammonia has a latent heat bubble 5 times bigger than other refrigerants. That means 5 times more refrigeration effect, per kilo of refrigerant, than HFC refrigerants.
Case Study of Industrial Refrigeration
The photo is during a visit after a period of neglect.
Leak Detection System Calibration
As a matter of urgency, we calibrated the ammonia leak detection system. It was in fault because of ammonia leaking over a long period of time, throwing it out of calibration. A working ammonia warning system was the most important part of this visit so far!
Compressor 'o' Ring Leaks
The ammonia was leaking from the 'o' rings on the compressor. This type of problem occurs more often on the discharge. Due to the heat, the 'o' rings become plastic like and flat- causing them to leak.
Compressor Remanufacturing
We lift and shifted the compressor to be remanufactured in our workshop. The rotors, with bearings, slide out still pressed into the casting, so it was straight forward to strip the compressor, replace the 'o' rings and shaft seal, then rebuild the compressor.
Condenser Fan Replacement
On running the plant, we found that most of the condenser fans needed replacement. The long period of time that the chiller had been off had allowed water to ingress into the fans. To fix the system, the fans and scaffolding were sent to site and the fans were replaced.
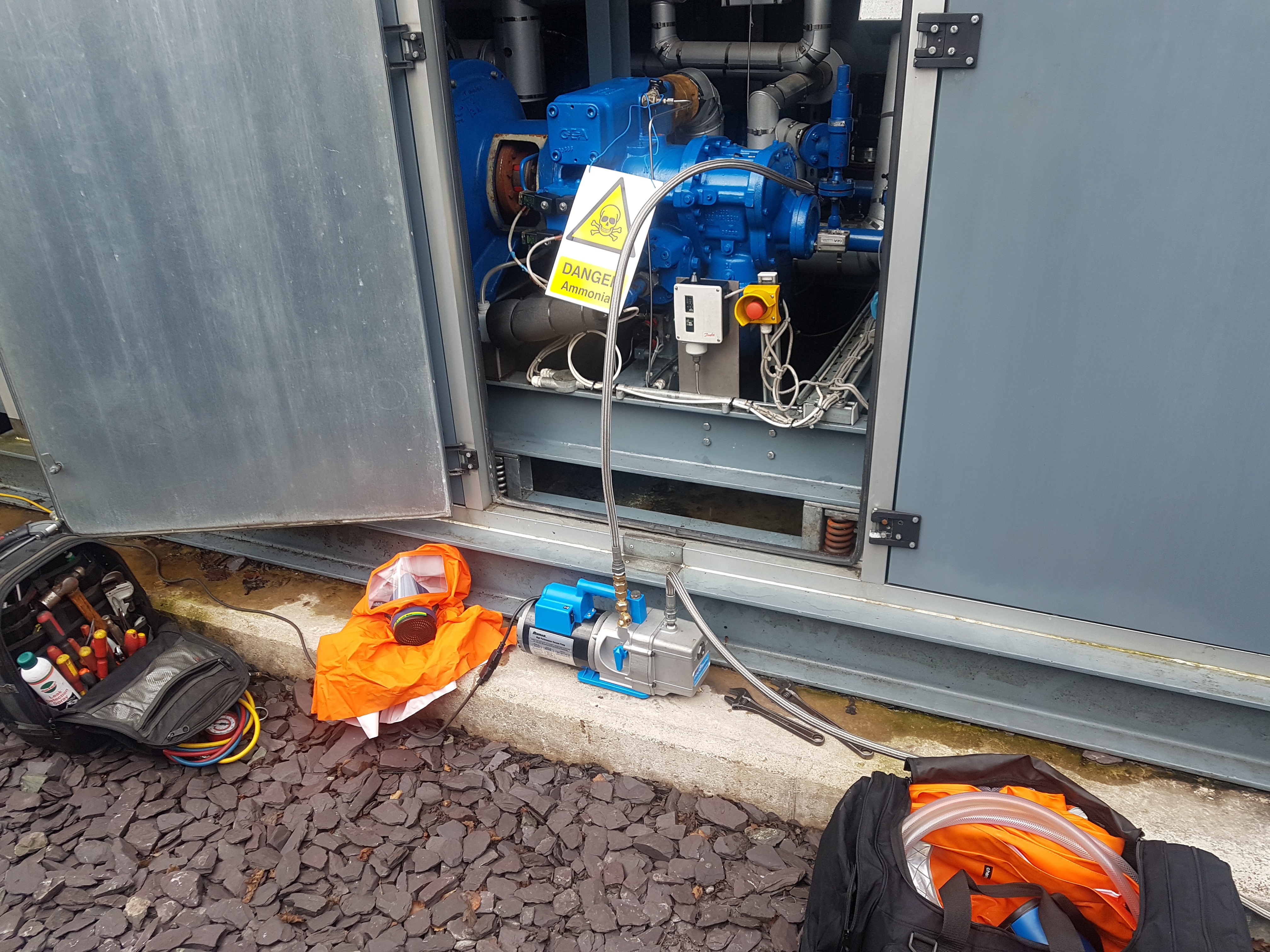
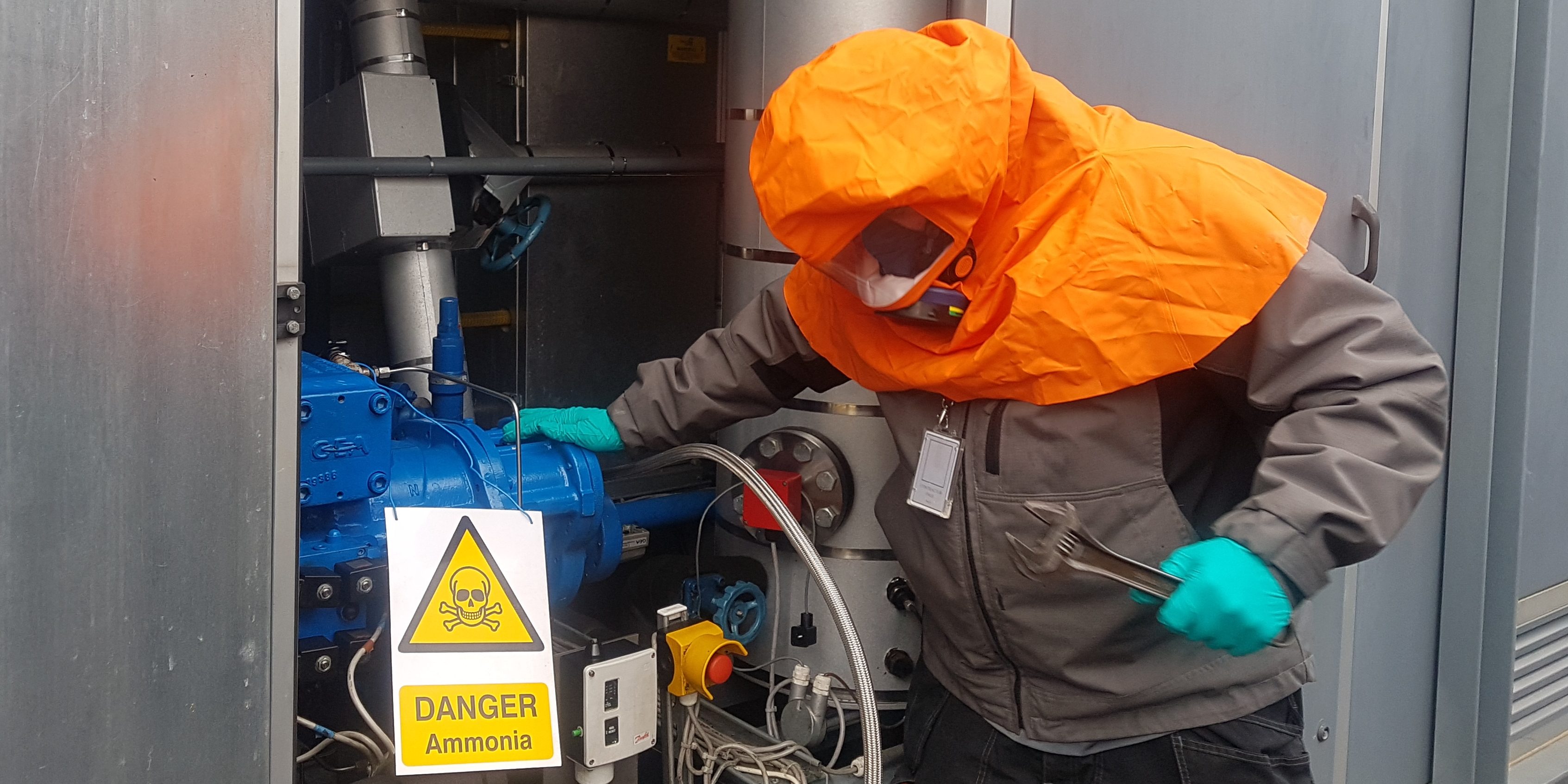
Alarm and Refrigerant Leaks
Maximus Chillers offers the complete package for your plant including...
Ammonia Alarm
In the event of a leak, the ammonia alarm is triggered and the plant shuts down. The machine brings a fan on which disperses the ammonia into air. The ammonia refrigerant then absorbs into the moisture in the air.
Leak Repairs
For large leaks: breathing apparatus and chemical suits are required to isolate the leak and allow time for ammonia dispersal. For small leaks: an escape hood is required in the work location. Our engineers repair the leak, then start the machine back up.
What We Offer for Industrial Refrigeration
A Lifetime of Experience
The work being carried out in the picture has to be done professionally to ensure minimum disruption in downtime. Between all the team here at Maximus Chillers we have a lot of industry knowledge. We have engineers who specialise in the different manufacturers of machine.
Parts and Materials
Maximus Chillers can source any part and material through our fast supply chain. Offering same day delivery for most parts. We can even upgrade your plant by fitting new parts
The Best Equipment
Good tools and equipment make the job go easy. Our equipment is the best available to our industry. When we work on your plant, you can rest assured in the quality of our equipment and the quality of our workmanship.
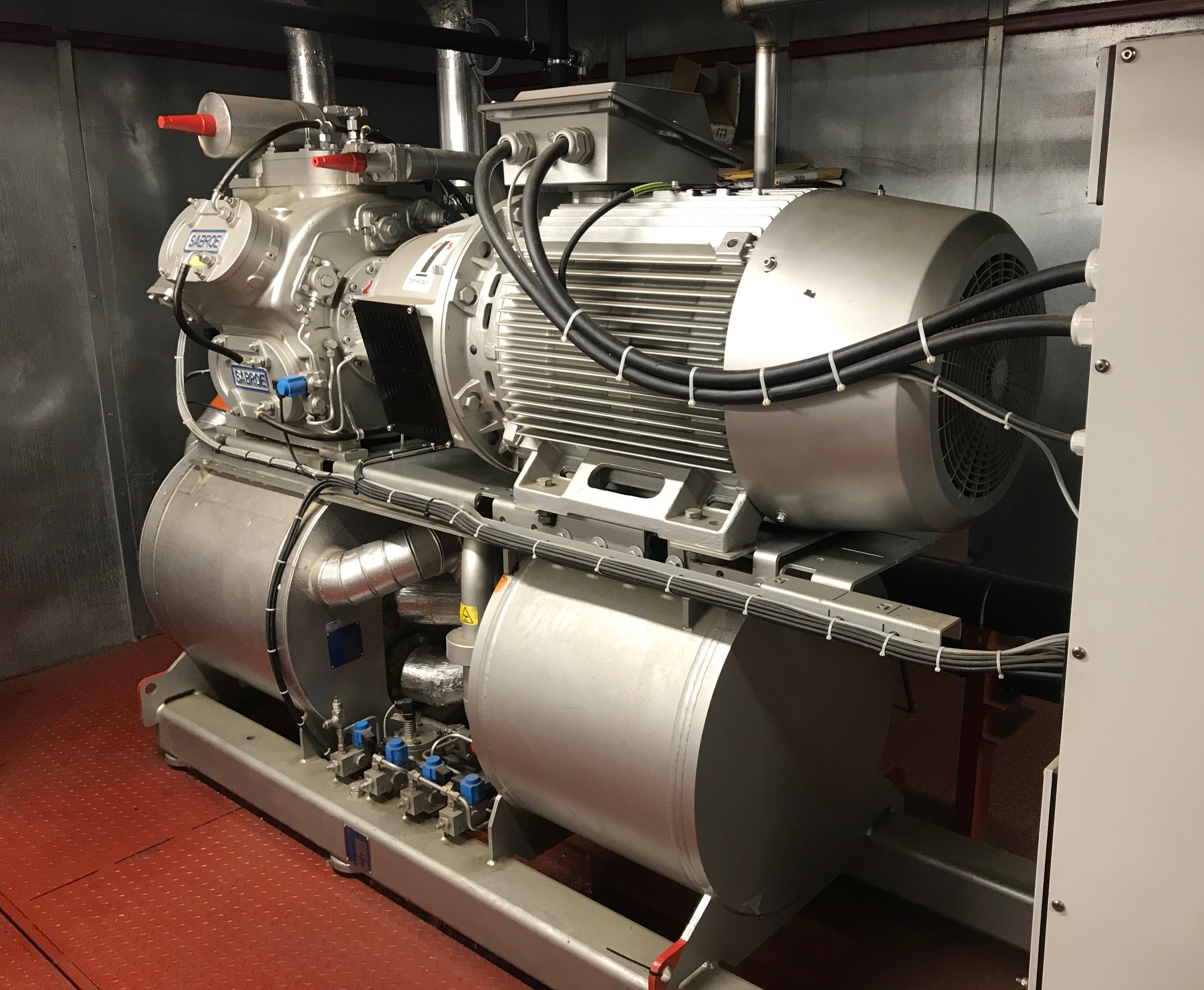
0161 237 3727service@maximuschillers.com ✎Contact Form
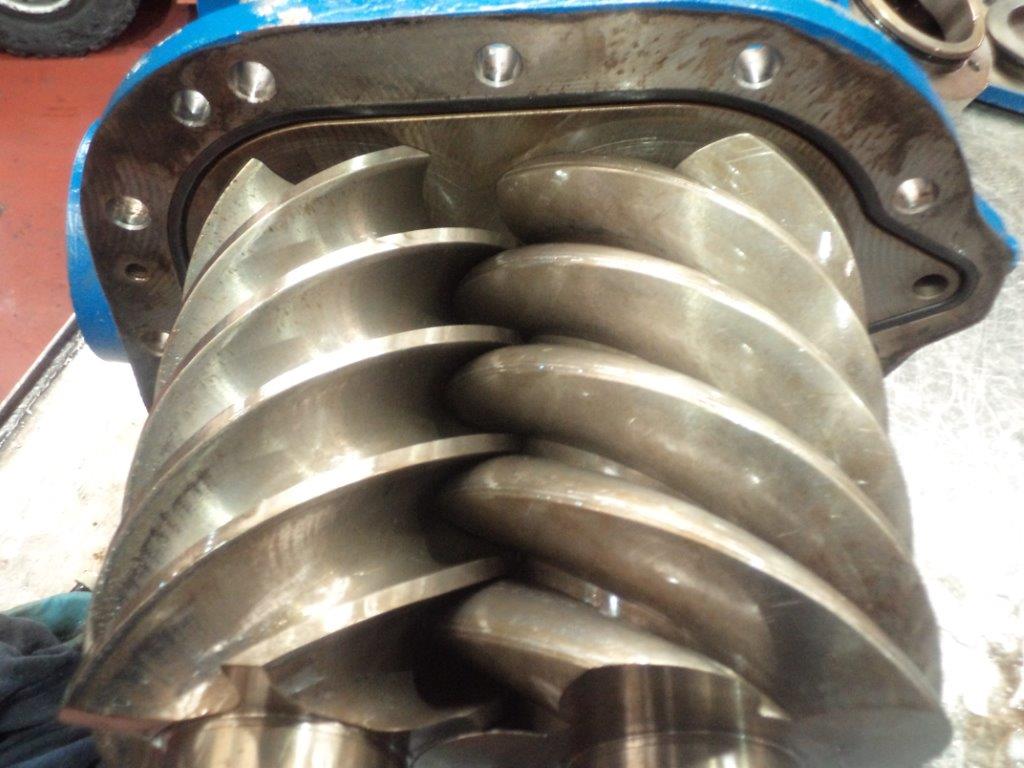
Why Choose Us for Industrial Refrigeration?
We have a capability that is second to none.
Manufacturer trained engineers.
National and international.
Next Steps...
Ring our Technical Support Desk to discuss your issues and requirements 0161 237 3727
Send an email through to service@maximuschillers.com
The Contact Form works and is monitored- try it!
Pipework
The use of steel makes ammonia pipework different as opposed to HFC chillers. Ammonia corrodes various metals and alloys. Steel, however, works well with ammonia.
HFC
These chillers are prone to leaks on the copper pipework. On the condenser, the copper expands and contracts- eventually rubbing through against the steel frame. Vibration related leaks are also common.
Ammonia
On an ammonia system, steel that is freezing then thawing on defrost or off cycles creates rapid rust formation and can lead to catastrophic failure of the pipework. Steel that is permanently frozen creates slower rust formation as the ice slows the oxidisation process. On a service visit, our engineers carry out metallurgic testing to gauge the integrity of the steel.
Tick Sheet for Industrial Refrigeration
We at Maximus Chillers believe that our detailed Tick Sheet is the best in the industry. It has taken years of development, every time there is a change in the industry- the Tick Sheet is updated. It has all the values and adjustments that can be checked to ensure the optimum, energy efficient performance of your plant. When an engineer is struggling during the fault finding, he uses the Tick Sheet as a reference- the fault will be on there somewhere!
Oil Return
Oil used to lubricate the compressor and ammonia are non miscible. That is to say: the refrigerant does not entrain the oil round the system and back to the compressor.
Reciprocating Compressors
On a system using reciprocating compressors: the oil mainly stays in the compressor.
Screw Compressors
Screw compressors work differently: the oil is discharged, so an oil separator is vital for the oil to return.
Oil Separator
Put simply: an oil separator makes it as easy as possible for a gas to get through, while as hard as possible for a liquid to get through. The oil drains to the bottom of the vessel and is pumped to above discharge pressure into the screw and bearings.
Oil Harvesting
During the maintenance visit: oil is harvested from the low side of the system. On modern systems, the oil return sensors and oil return solenoids ensure most of the oil gets back. This is assuming that the system is running otherwise okay- if there are refrigerant issues- oil return issues will follow.
People also like these pages:
Ammonia Refrigerant Recovery

Call Out
Schedule a site visit today!