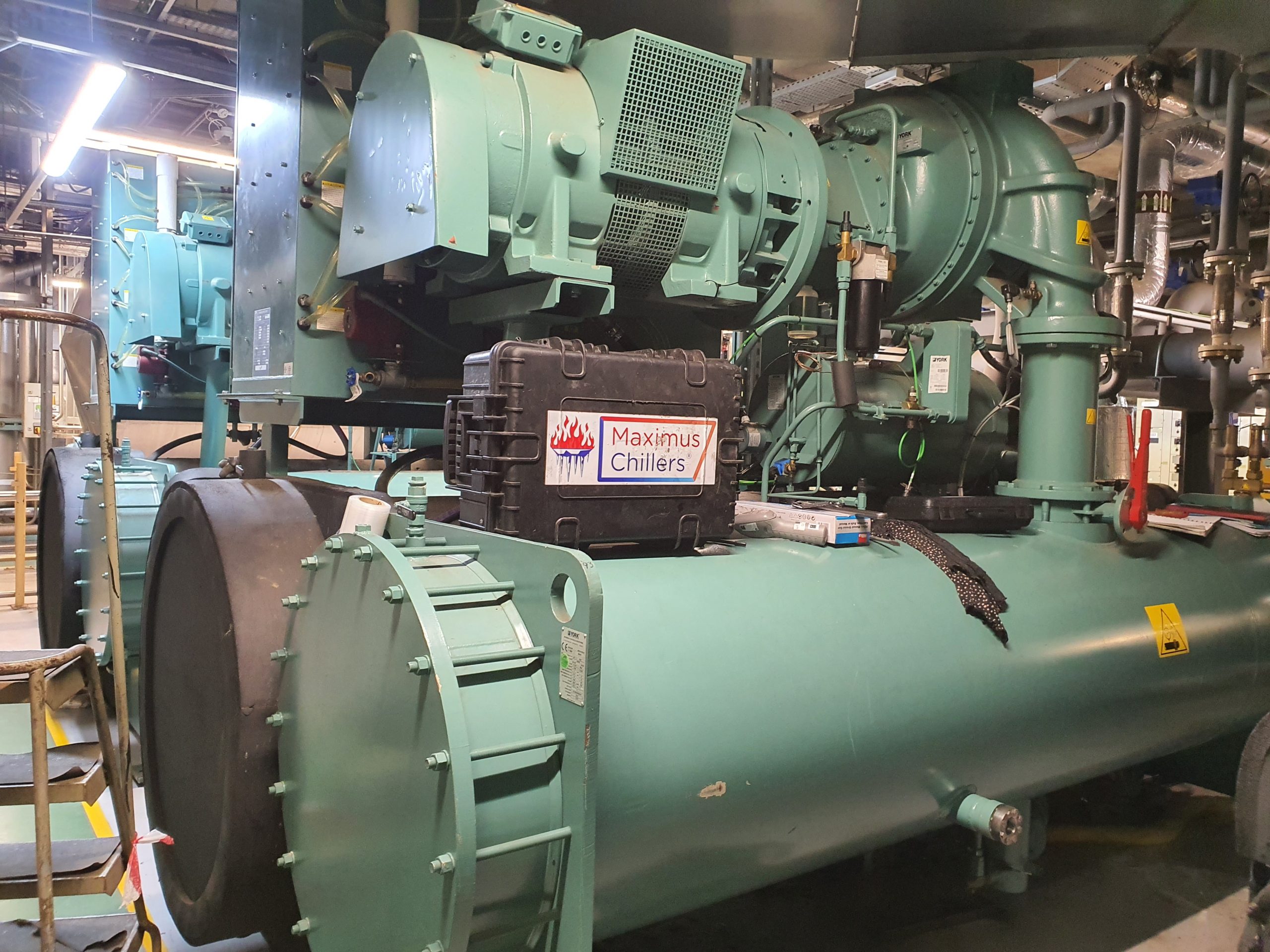
The Service, Maintenance and Repair of Centrifugal Chillers
Maximus Chillers are a specialist centrifugal chillers company- national and global. With maintenance packages and a 12 month warranty on all our remanufactured chiller compressors.
Centrifugal compressors are not positive displacement systems like screw and reciprocating compressors. Therefore, they have a lower volumetric efficiency. They are used in applications such as large industrial processes or district cooling.
Shaft Seal
A popular compressor type is open drive. The shaft seal needs to be replaced when it shows signs of wear. Because the issue is noticed during the service visit, the repair can be arranged to take place during a factory shut down.
Tube Fouling
Tube fouling lowers efficiency on centrifugal chillers. This can lead to safety shut down and loss of production. A visit can be arranged to dismantle the shell and tube heat exchangers and repair the issue.
Oil Return
On the major maintenance visit, the oil filter is cleaned or replaced according to the type. This allows the effective lubrication of the bearings for the high and low speed shaft. The low speed shaft is driven by the motor. The high speed shaft spins the impeller.
What We Offer for Centrifugal Chillers
We have years of industry experience with the repair and maintenance of centrifugal compressors. Our remanufacturing facility is complete with a gantry crane for the removal of compressor components.
Next Steps...
One of our engineers will be happy to discuss your requirements. We will then put together a maintenance package. Send us some pictures of your plant. The data plate gives us information, such as, the type and quantity of refrigerant. A picture of the whole chiller gives us a feel for the plant.
0161 237 3727
service@maximuschillers.com
Case Study of Centrifugal Chillers
A large centrifugal compressor was found to be surging under low load conditions at a chemical plant. On start up, the oil pumps were 'pre lubeing' the compressor bearings, but the oil pressure was not building up. This is because the oil was dropping through the worn bearings and into the sump.
Call Out
The call out was attended on a Sunday. Even though out of hours, full assistance was available to our engineer through our Technical Support Desk. He diagnosed that the thrust bearings had failed and the impeller had ground against the casting.
Remove Ancillaries
The Quote had been approved by the end user, so a visit was arranged to remove the ancillaries. The compressor was valved off and fittings removed. Then, the discharge and suction pipes were unbolted and the gaskets removed.
Lift Out
The lift and shift team arrived at 10 ‘o clock on Wednesday. They are a joy to watch as they do this type of job all the time- they had the compressor out in a flash! They palletised the compressor, then used a forklift truck to lift it onto an articulated truck which had arrived for the transportation.
Centrifugal Chiller Compressor
The useful life of the centrifugal chiller had been prolonged with a full overhaul of the compressor in our workshop. 12 month warranty on all of our compressors. After the compressor was pressure tested, it received a full re paint.
Lift In
The same lift and shift team carried out the lift in. They used a forklift truck to remove the compressor from the truck. The compressor was then lifted to a compound where a lifting dolly was used to take the compressor down a path to the chiller. They set up their portable lifting equipment next to the chiller and lifted the compressor into place. Securing it to the shell and tube evaporator with holding down bolts. These bolts were then torqued to the recommended value.
Fit Ancillaries and Testing
New gaskets were made to measure by our bespoke gasket supplier. They had delivered them to our workshop a couple of days earlier. We rubbed them with a special compound to aid with the seal. We then torqued up the bolts to the discharge and suction flanges. The fittings were reinstated using vibration resistant thread locker that can withstand the temperature difference on the compressor. That was two years ago now and it is still running perfectly.
0161 237 3727
service@maximuschillers.com
Why Choose Us for Centrifugal Chillers?
We offer the highest level of customer service and technical ability. Any Chiller- Any Problem- Any Part- Any Refrigerant- Anywhere- The MAXIMUS ADVANTAGE™
We offer a practical approach to the upkeep of your plant. We can get your chillers to settle down and have less issues to deal with. Maintenance schedules are rationalised, so that only essential works are carried out. We have a team of engineers who are trained in the art of making machines run efficiently. We make your chillers younger with the ongoing maintenance by Maximus Chillers.
Maximus Chillers are specialists in the niche of centrifugal chiller maintenance. We are a distributor for the various types of chillers, however, we seldom sell chillers. This is because the whole lifetime of experience of the company has solely been focused on service, maintenance and repairs. This is what we do best. We will always resolve the problem in a short time with the minimum of cost to the end user.
Call Out
Schedule a site visit today!