In this article a bespoke chiller with ammonia refrigerant is having troubleshooting carried out to identify the faults. Read below to have a look into the various issues that commonly occur on this machine…
News Article No.19
Chiller Troubleshooting of Low Oil Level
There are times when this machine experiences a low load condition. This is because another chiller is also available as well as free cooling.
Building Management System
The BMS regulates the sequencing of the chillers, the pump sets, the water system valves and the free cooling. We found after troubleshooting that, especially in the winter, the BMS can be slow to react. This causes the chiller to continue running with low load.
Slide Valve at 0%
During a low load condition, the compressor has been designed to run with the slide valve at 0% to prevent too many start ups. These start ups would cause a higher amount of electricity to be used because of the amps being drawn to get the compressor going. Although the compressor uses star/ delta contactors which are a soft start, the repeated starts would still draw a lot more amps. Therefore, the compressor continuing to run at 0% is a lot more efficient.
Oil Pump and Oil Level
When this condition occurs, however, the oil pump continues to suck and then discharge the oil. Eventually, the level in the oil separator drops to below the oil level switch and the alarm is triggered. The photo shows this switch which is a float on a stem. The circuit is completed when the float is at the top of the stem. When the float slides down the stem- this triggers the alarm.
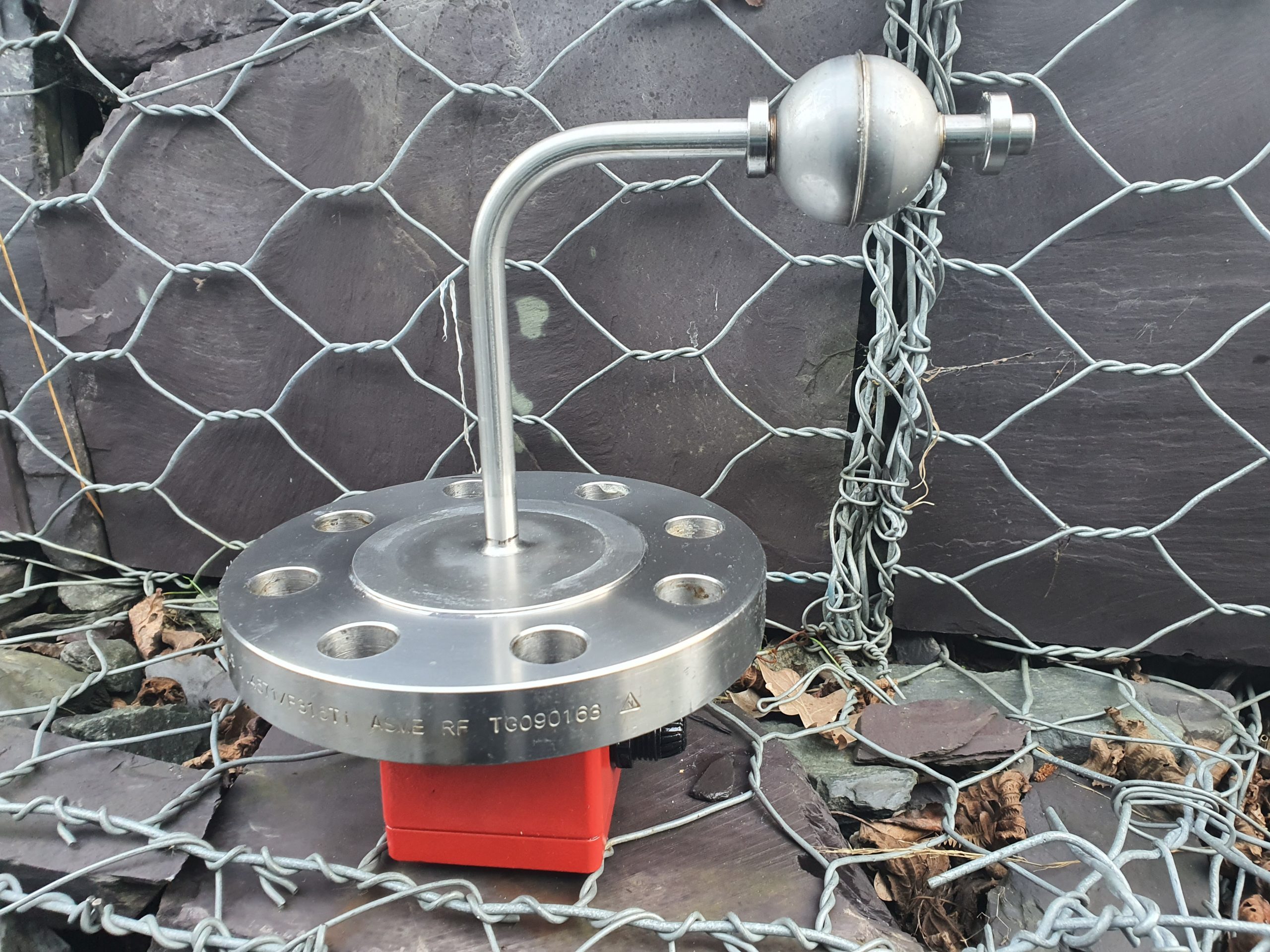
The Repair
Specialist ammonia resistant personal protective equipment, or PPE is donned by our engineers. Then, ammonia grade oil is pumped in so as to complete the circuit of the switch. After a start up, the same amount of oil has to be taken back out at the other end of the system using the dead man’s valve. This is a valve on the bottom of the economizer which shuts by itself using a spring.
0161 237 3727
service@maximuschillers.com
Chiller Troubleshooting of Oil Filter Differential
When this alarm occurs, you can see the discharge pressure remain at 8 bar and the pressure after the oil filter slowly drop off to less than 6 bar. When interrogating the program, the oil pressure differential trip out is set to 2 bar. After this differential is exceeded, a timer starts to prevent spurious trip outs occurring if the differential pressure is exceeded momentarily. If the differential pressure continues to be exceeded after the timer has timed out- the machine goes into a fault condition which needs a manual reset.
Chiller Troubleshooting Inspection
When removing the cover for the compressor enclosure, the discharge oil pipe can be seen going into the oil filter. An oil pressure transducer can be seen on the far side of the filter.
Contaminants
After the above troubleshooting, it was found that with this kind of system, the oil becomes contaminated with sludge and debris from around the system. Over time this builds up behind the oil filter and so causes the trip out.
The Repair
The repair requires the oil filter to be valved off on either side. Then, full length PPE suitable for the handling of ammonia is required along with beathing apparatus. Each of our engineers carries a portable ammonia alarm and state of the art ammonia handling equipment. We also produce our own ammonia oil filters which we keep on the shelf at Head Office. Give our Technical Support Desk a bell for further assistance.
0161 237 3727
service@maximuschillers.com
Chiller Troubleshooting of Slide Valve Potentiometer
This is a 4-20mA sensor which detects the position of the slide valve. 4mA being shut and 20mA being open. We attended a call out to troubleshoot the alarm message of “slide valve failed to reach the closed position” There is a spring on the end of the slide valve which is used to push it to the closed position when the compressor is off. We decided to activate the drain and fill solenoids which are used to open and close the slide valve. Still the same fault persisted. Having decided that the slide valve was indeed at its closed position, we decided to calibrate the closed and also the open position of the valve.
The Repair
The compressor was valved off and our engineer donned the necessary PPE. The sensor stem was removed from the end of the spring which is attached to the slide valve. A lock nut is available to hold the stem at the required position. This was found to have vibrated loose and so causing the problem. The correct length was set on the stem and the lock nut was re tightened. After rebuilding the end of the compressor, the valves were opened and the compressor checked for leaks. Then, the system was run tested using the manual load and unload buttons on the controller. A good read back was recorded and the machine went into seamless operation.
Chiller Troubleshooting of Ammonia Leak Detection System
This device is stand alone from the chiller and has its own uninterruptable power supply. This UPS is needed so that when there is a power failure to the building, the alarm would still function. There are 2 toxic gas sensors and 2 fire detectors fitted in different locations on the chiller.
Out of Calibration
When we took over the contract 5 years ago, the chiller had been in fault for some time with a leaking shaft seal. After troubleshooting the problem, we found that the small amount of ammonia leaking from the shaft seal and onto the sensor had knocked it out of calibration. This is because the sensor needs to be calibrated to a zero ammonia atmosphere as a reference point.
The Repair
After changing the shaft seal, we decided to change all 4 of the sensors and plug the detection system into our laptop for calibration. The benchmark was set for each sensor, then each sensor was bump tested to the required parts per million of ammonia to ensure that the detector trips when it should. All read backs were found to be okay, so we completed the calibration certificate which the customer keeps in his chiller file.
Related Articles:
Industrial Refrigeration Oil
Industrial Chiller Maintenance
Industrial Refrigeration Ammonia
Industrial Refrigeration Sludge
Hit the Tags below to navigate your way to our extensive library of further reading on this subject.
Watch a video about chiller faults troubleshooting from The Engineering Mindset on Facebook